Le projet porté par l’entreprise Européenne de Biomasse est entré dans sa phase opérationnelle en février 2021 sur son site FICA HPCI de Pomacle-Bazancourt (Marne). Objectif : produire 125 000 tonnes de Green Pellet par an.
«Un grand moment d’émotion ». Pour Jean- Baptiste Marin, la sortie des premiers pellets HPCI des machines de son usine FICA de Bazancourt, dès le 19 février 2021, est la première étape de concrétisation d’un projet dantesque. « Cette usine, nous l’avons tellement rêvée que la voir en fonctionnement est indescriptible », poursuit le Pdg d’Européenne de Biomasse, porteuse du projet. Il faut dire que cette société indépendante fondée en 2004, a mis au point pas moins de 16 brevets, une quinzaine d’années de travail et un investissement de 110 millions d’euros pour parvenir à la phase de fabrication industrielle de son Green Pellet HPCI, un granulé de bois innovant, sans poussière, sans émission de CO, hydrophobe et dont la combustion émet davantage d’énergie que ses concurrents classiques. Une première mondiale industrielle.
Si les travaux ont pris six mois de retard au printemps 2020, le chantier ayant été mis sous cloche en raison de la pandémie, la production du Green Pellet n’a donc démarré qu’en février 2021, souligne Jean-Baptiste Marin. Depuis, la mise en œuvre du circuit a été activée, tout comme les lignes de production. Et le Green Pellet est en cours de production. « L’usine est encore en phase de réception mais toute une série de tests de production sont organisés. Aujourd’hui on règle les machines, on affûte les couteaux ». L’usine devrait stopper sa production une quinzaine de jours en juin pour les derniers réglages et pouvoir produire à plein dès cet été pour atteindre 125 000 tonnes par an en vitesse de croisière. La production du site devrait répondre, selon le Pdg à une demande croissante en pellet, en raison notamment des nouvelles réglementations liées à l’interdiction des chaudières à fioul et du gaz dans les constructions neuves.
CRÉATEURS DE FILIÈRE VERTE LOCALE
Pour autant, le Green Pellet ne se positionne pas directement en concurrence des granulés de bois classiques, ne serait-ce que par son positionnement commercial. « Nous ne visons pas une clientèle grand public, nous visons plutôt les réseaux de chaleur et le secteur du résidentiel. Nos cibles idéales sont les communes qui utilisent encore du fioul ou du gaz et qui veulent un combustible moins cher et plus simple à utiliser ».
Quant à l’implantation du site à Pomacle-Bazancourt, elle ne doit rien au hasard. « On est dans un creuset agro-industriel extrêmement important. Nous sommes dans une région où les gens savent que sous une cheminée il y a des gens qui travaillent et qui inventent ». Question approvisionnement, l’usine mise sur l’extra-local en utilisant une biomasse entièrement traçable et issue de forêts situées à moins de 100 km de Reims. D’ailleurs, inutile de chercher de polémique sur l’éventualité d’une déforestation massive de bois d’œuvre pour alimenter l’usine à Green Pellet : le modèle économique HPCI repose sur l’utilisation de bois bon marché : « Nous recherchons soit des premières coupes ou des feuillus locaux, soit des bois malades ou stressés, soit des bois non utilisables dans d’autres industries, souligne le Pdg. Nous sommes créateurs de filière verte. Nous misons sur l’économie circulaire, sur la création d’emploi en zone rurale et sur un équilibre budgétaire pour que les investisseurs puissent développer le modèle ».
Le Green Pellet est, selon ses inventeurs,un produit vert de bout en bout de la chaîne de production. « Notre produit assure un rendement de 100% de la matière utilisée : il ne reste aucun déchet », insiste Jean-Baptiste Marin, qui évoque même « une usine du XXIe siècle, qui n’utilise pas d’eau de la nappe phréatique et qui n’émet ni odeur ni bruit ».
Si aujourd’hui une cinquantaine de personnes assurent la mise en route du site, le projet doit, à terme employer pas moins de 350 personnes, entre l’usine, les employés en forêt, les chauffeurs et les spécialistes de la logistique. « Notre métier est de vendre la technologie à des usines qui produiront le Green Pellet », explique le Pdg de la société, très attaché à la réindustrialisation du pays, avec le soutien de partenaires financiers et industriels intéressés par l’utilisation de cette technologie.
D’ailleurs, Européenne de Biomasse compte bien dupliquer son modèle, et commence à intéresser des investisseurs qui se montrent attentifs à l’aventure Green Pellet. « Nous avons pour objectif de développer notre modèle en France, en Europe et à l’International. Nous sommes actuellement en phase de développement d’une usine identique à Fessenheim (Alsace) pour dupliquer cette première mondiale dans le Grand Est, qui est notre berceau ». De là imaginer que le Green Pellet puisse remplacer un jour le nucléaire…
Une entreprise de partenariats
FICA HPCI est l’entreprise qui porte le projet de la production du Green Pellet. Elle est détenue à 85% par Meridiam, à 15% par la Caisse des Dépôts et à 5% par Européenne de Biomasse.
LE GREEN PELLET REMPLACE LE BLACK PELLET
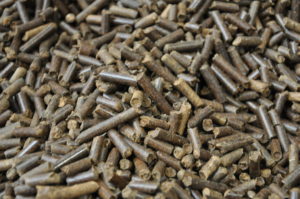
À l’annonce du projet industriel marnais en 2018, le produit mis en avant par Européenne de Biomasse était baptisé Black Pellet. Un nom aujourd’hui abandonné au profit du Green Pellet, un choix assumé par les équipes de Jean-Baptiste Marin. « Le Black Pellet représente tout ce qui n’a pas marché depuis 10 ans », sourit-il. « Certains industriels qui ont essayé les techniques de torréfaction ou de « steam explosion » m’ont avoué avoir perdu plusieurs dizaines de millions d’euros ».
De quoi donner envie aux investisseurs de conjurer le mauvais sort et de rebaptiser le Black Pellet en Green Pellet. Une consonance plus verte pour un produit qui coche de toute façon toutes les cases de l’écoresponsabilité.
Issue de 16 brevets, la technologie de « vapocraquage » développée pour le HPCI Green Pellet est une grande première mondiale industrielle. Elle consiste à soumettre de la biomasse à une très forte pression dans un réacteur. Une fois relâchée subitement, les molécules d’eau sont vaporisées et la matière est transformée en poudre. Résultat : une particule absolument résistante à l’eau utilisée pour obtenir des pellets parfaitement hydrophobes.