Spécialisée dans la fabrication d’éléments composites, la PME de Labège veut s’ouvrir à de nouveaux secteurs d’activité et s’agrandir.
Spécialisée dans la fabrication d’éléments composites pour les secteurs de l’aéronautique, de la défense et du spatial, ST Composites fabrique des pièces et sous-ensembles pour des donneurs d’ordre principalement situés dans la région Occitanie, tels Stelia Aerospace, Mecahers-Mecachrome, Safran Power Units, Thales Alenia Space, l’Irt Saint Exupéry ou encore le CEA Gramat. Implantée à Labège depuis 1998, la PME emploie aujourd’hui 30 salariés et réalise 3 M€ de chiffre d’affaires.
Soumise durant plusieurs années à un plan de redressement judiciaire, ST Composites en est sortie plus forte et mieux armée pour affronter la crise économique liée à la chute des commandes en début d’année. Comme beaucoup de sous-traitants aéronautiques, son activité est en baisse de 50% en 2020. Fort heureusement, en 2019, ST Composites avait amorcé un processus de diversification de ses activités vers le médical, les télécommunications, le luxe et l’armement. L’entreprise ne manque pas de projets pour 2021. Elle compte bien concrétiser le lancement d’une nouvelle société exclusivement dédiée à l’univers du luxe qui développera un produit en propre associant une nouvelle technologie composite issue de l’aéronautique, du spatial associé à l’aéropostal pour une clientèle cette fois-ci de particuliers.
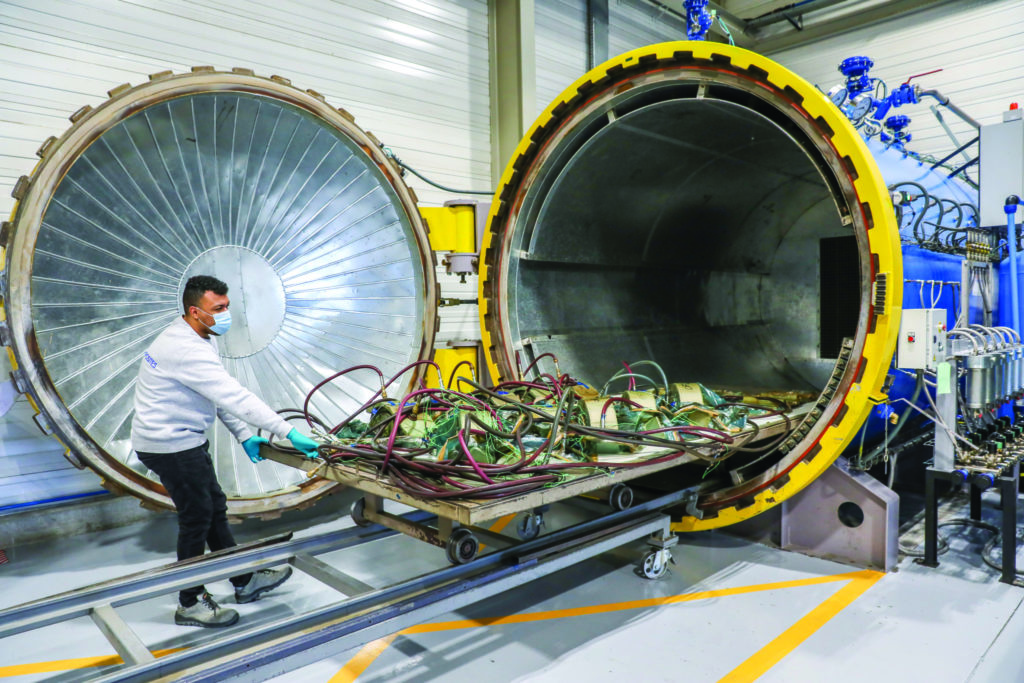
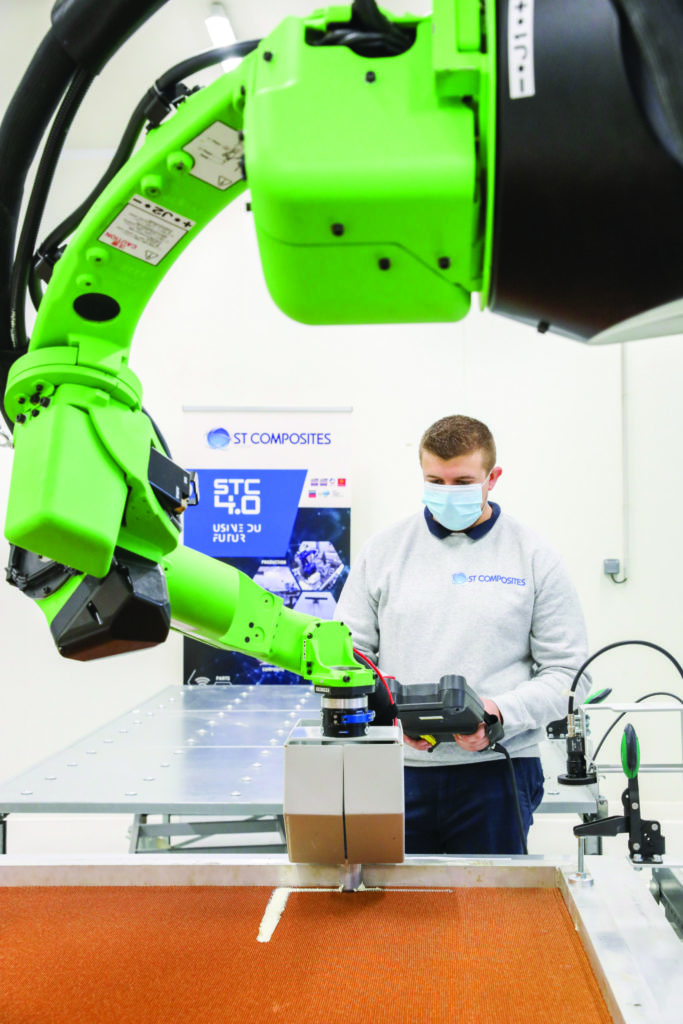
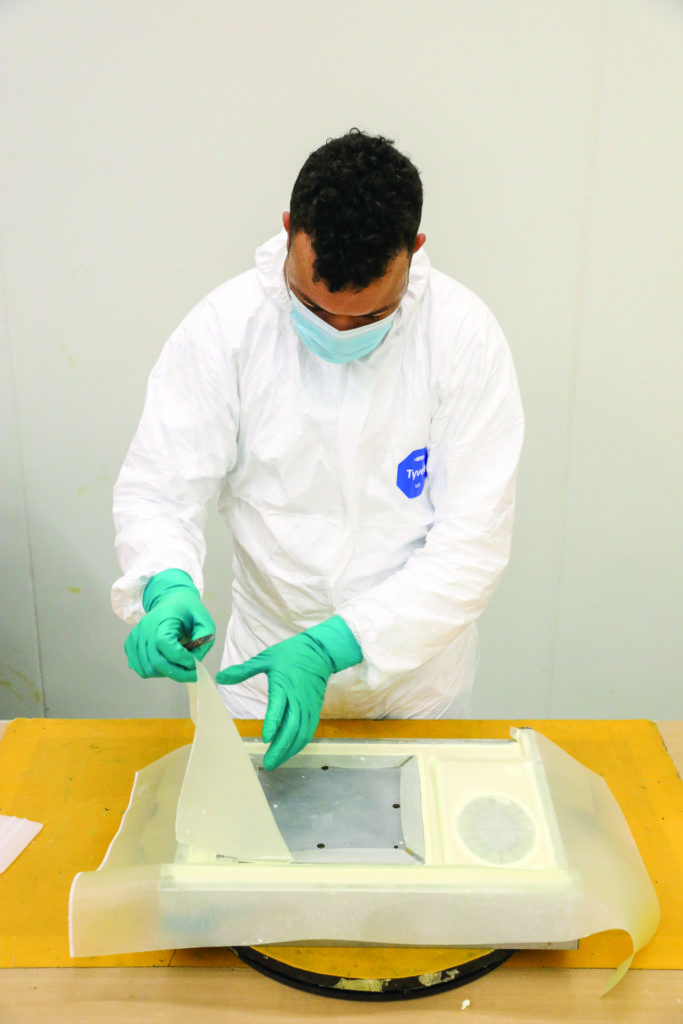
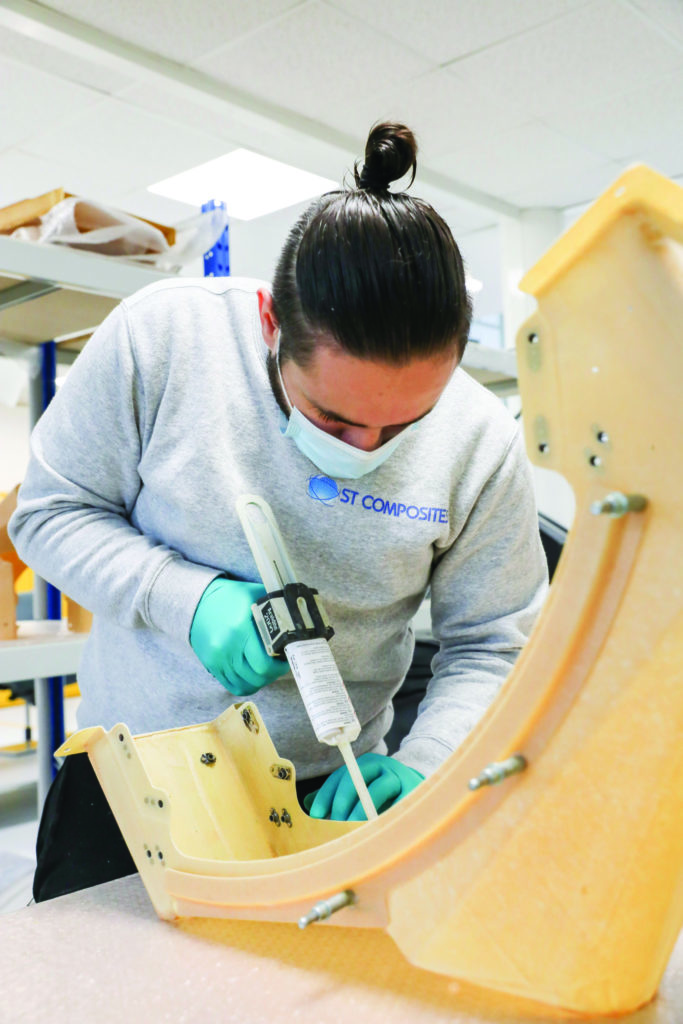
Dans le cadre de sa transition vers l’usine 4.0, ST Composites digitalise sa production. L’entreprise vient en effet de se doter d’une nouvelle salle de drapage de panneaux sandwich cobotisée de 150 m2. Une révolution puisque la fabrication du composite est essentiellement manuelle : moulage, drapage, jusqu’à l’assemblage final, toutes les étapes se déroulent entre les mains des collaborateurs.
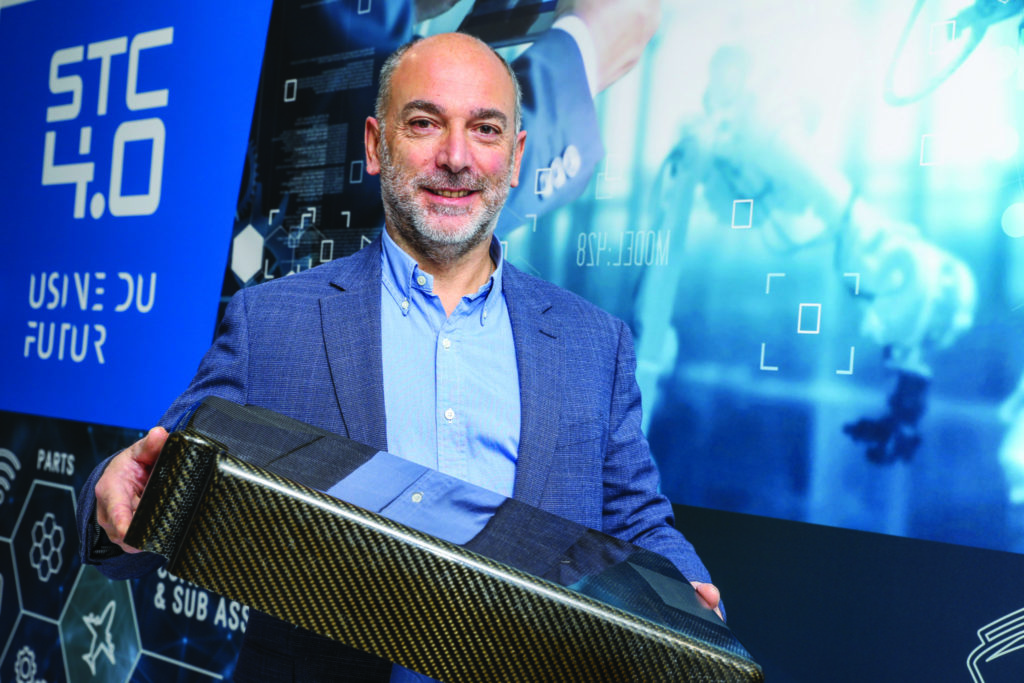
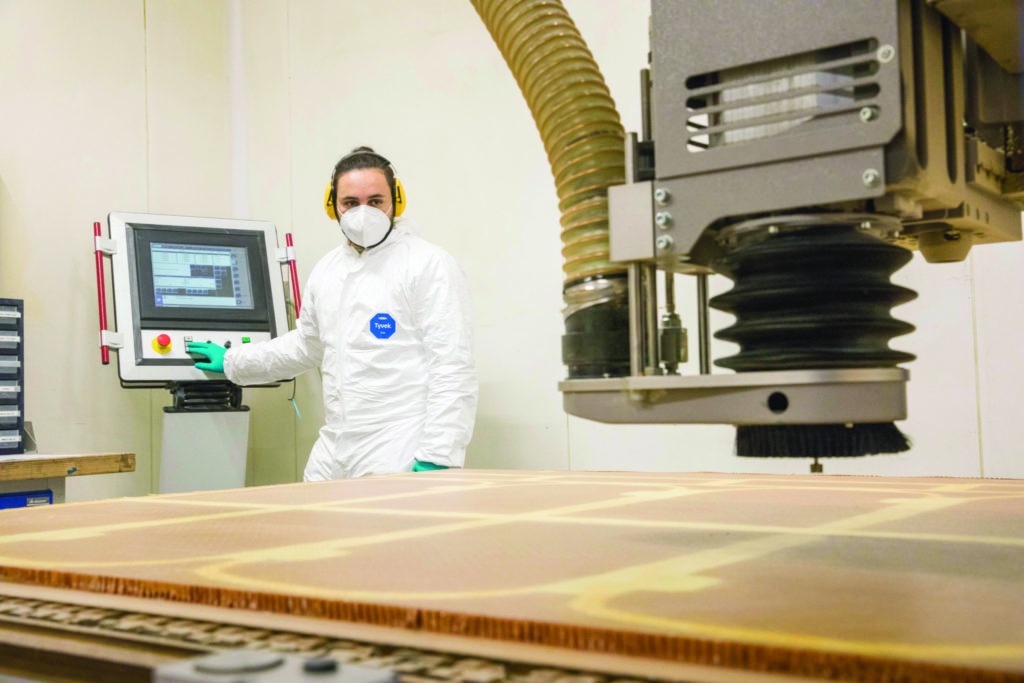
Stéphane Trento, ingénieur de métier, est président fondateur de ST Composites. Pendant la phase de redressement commencée il y a cinq ans, il a fallu être attentif à la moindre dépense, améliorer la compétitivité, sensibiliser les effectifs (ce qui a préparé les équipes à être plus agiles) et ce qui les a aidés à passer les difficultés liées à la pandémie. Le PDG, qui prévoit une sortie de crise courant 2021, espère doubler son chiffre d’affaires d’ici fin 2022 et porter son effectif à une cinquantaine de personnes. Ici, le centre d’usinage trois axes découpe un panneau sandwich d’aménagement de cabine.
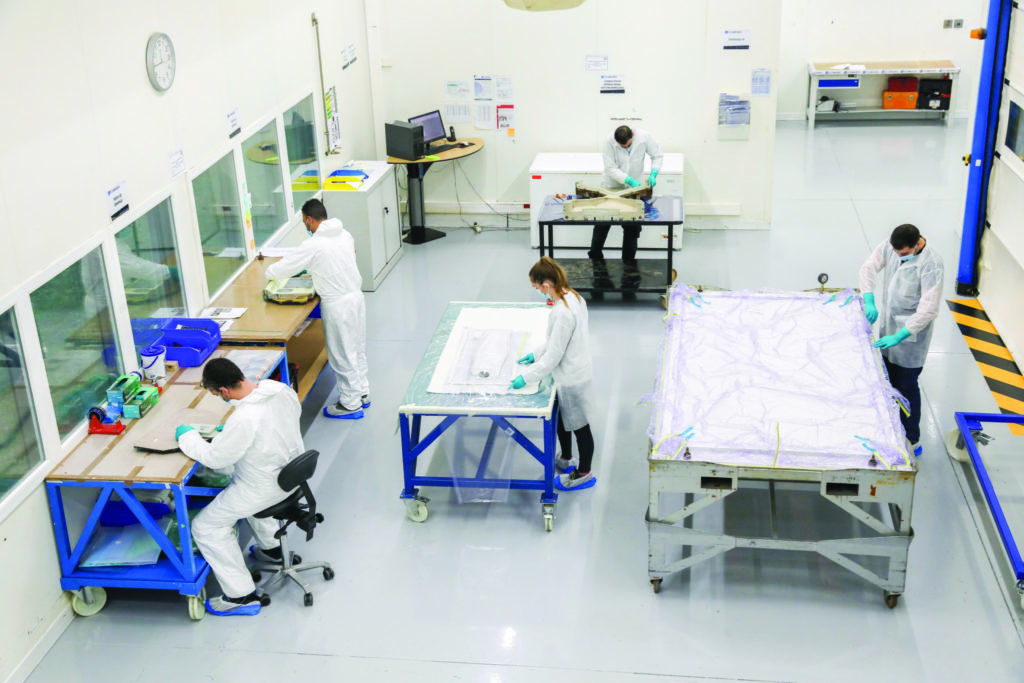
Cette salle blanche, ISO 7 de 150 m2, abrite essentiellement les activités de découpe de tissus préimprégnés et de drapage. 2021 sera l’année de l’agrandissement pour ST Composites. La construction d’un 3ème bâtiment de 1000 m supplémentaires est en effet prévue. Il sera dédié a la production digitalisée et robotisée de nouveaux services et prestations.